Inventory Replenishment Planning - Everything To Know
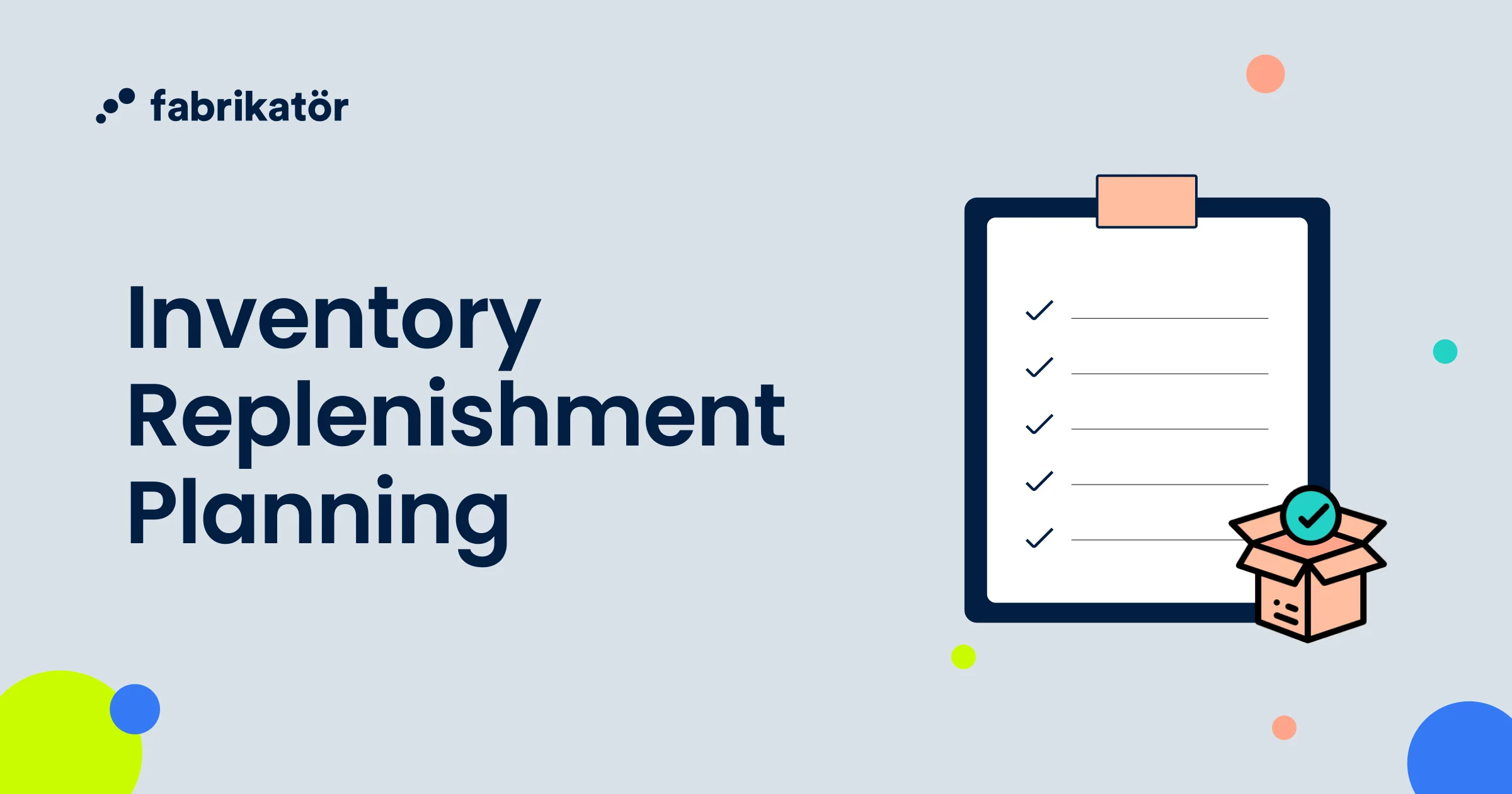
Managing inventory is crucial for the efficiency and profitability of your business.
That’s why exploring strategies like just-in-time replenishment and demand forecasting can help ensure your shelves are stocked while minimizing overstock and waste.
In this article, we’ll explore inventory replenishment planning, why it matters, the steps to create an effective plan, and the challenges you might face along the way.
Let’s get started!
What is inventory replenishment planning?
Inventory replenishment planning ensures that your business maintains the right stock level to meet customer demand without overstocking or running out of essential items.
It involves analyzing sales patterns, understanding lead times, and forecasting future demand to determine when and how much inventory to restock.
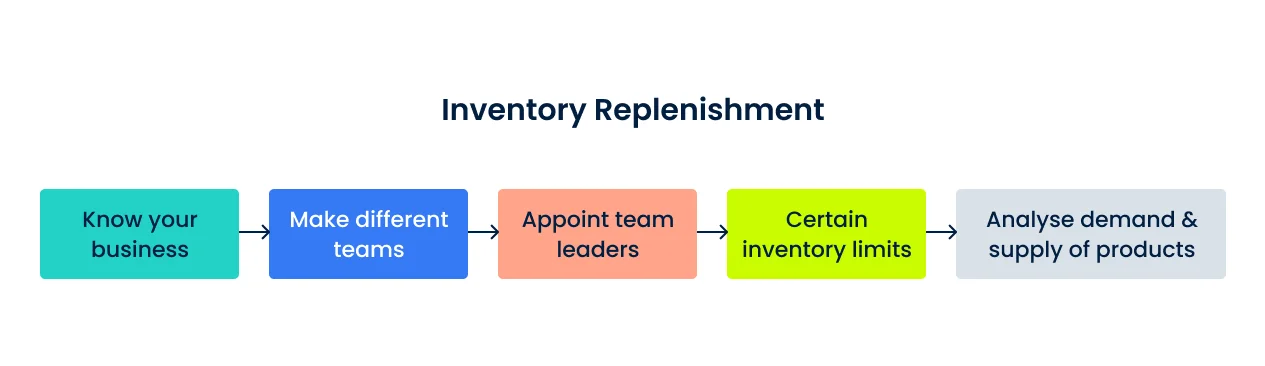
Effective replenishment planning helps businesses streamline operations, reduce storage costs, and enhance customer satisfaction by minimizing delays or shortages.
When to use inventory replenishment planning?
Inventory replenishment planning keeps operations running smoothly and meets customer demand. Let’s check some use cases of inventory replenishment planning:
1️⃣High sales periods: Plan replenishment during peak seasons to avoid stockouts and maximize sales opportunities.
2️⃣Managing seasonal demand: Align inventory with seasonal trends to minimize overstock and stockouts.
3️⃣Optimizing storage costs: Replenish stock strategically to balance inventory levels and reduce storage expenses.
4️⃣ Handling long lead times: Use planning to mitigate supplier delays and maintain steady stock availability.
Inventory replenishment planning benefits
Inventory replenishment planning offers several advantages that help businesses manage stock efficiently and improve overall performance:
1️⃣ Minimizes stockouts: Ensures products are available when needed, preventing missed sales opportunities.
2️⃣ Reduces overstock: Avoids excess inventory, lowering storage costs and waste.
3️⃣ Improves cash flow: Helps optimize purchasing decisions, freeing up cash for other business needs.
4️⃣ Enhances customer satisfaction: Maintaining product availability leads to better customer experiences and loyalty.
5️⃣ Streamlines operations: Automates restocking processes, saving time and reducing manual errors.
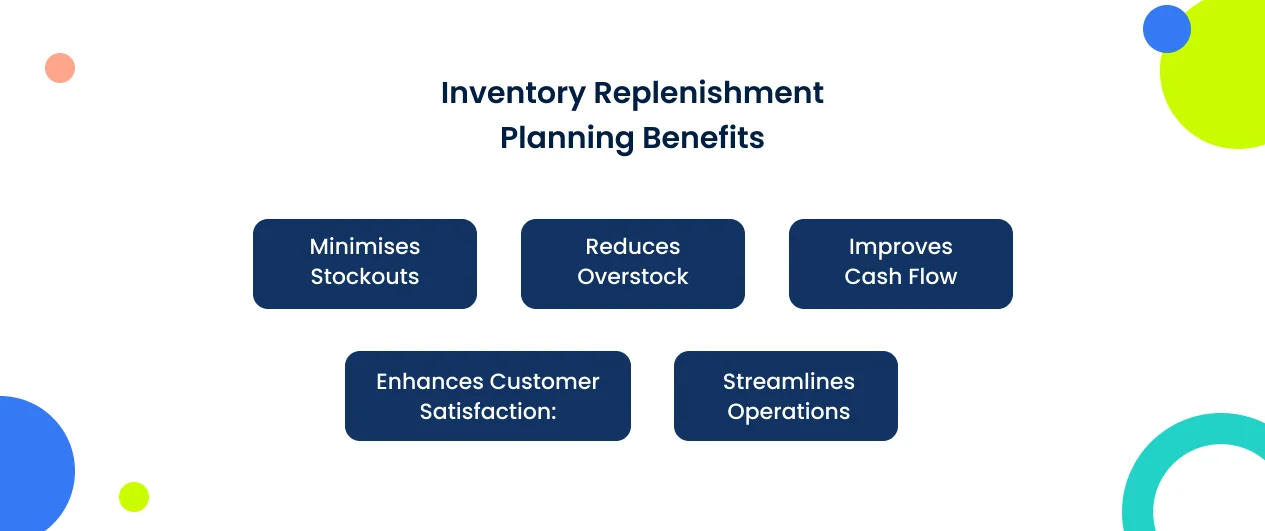
Common inventory challenges & how replenishment planning resolves them?
Effective inventory management comes with several challenges that businesses must address to maintain smooth operations and meet customer demands. Those challenges include:
1️⃣Spreadsheet-based replenishment process: Requires manual data imports and manipulation and is prone to errors and inefficiencies.
2️⃣Lack of visibility in incoming inventory: This prevents merchants from replenishing stock effectively, leading to poor inventory management decisions.
3️⃣Long supplier lead times: It makes maintaining consistent stock levels difficult, risking operational delays.
4️⃣ Inaccurate demand forecasting: Disrupts supply chains, leading to excess inventory or stock shortages.
5️⃣ Stockouts: Result in lost sales and dissatisfied customers, damaging business reputation and revenue.
6️⃣ Overstocking: Ties up valuable capital and increases storage costs, reducing overall profitability.
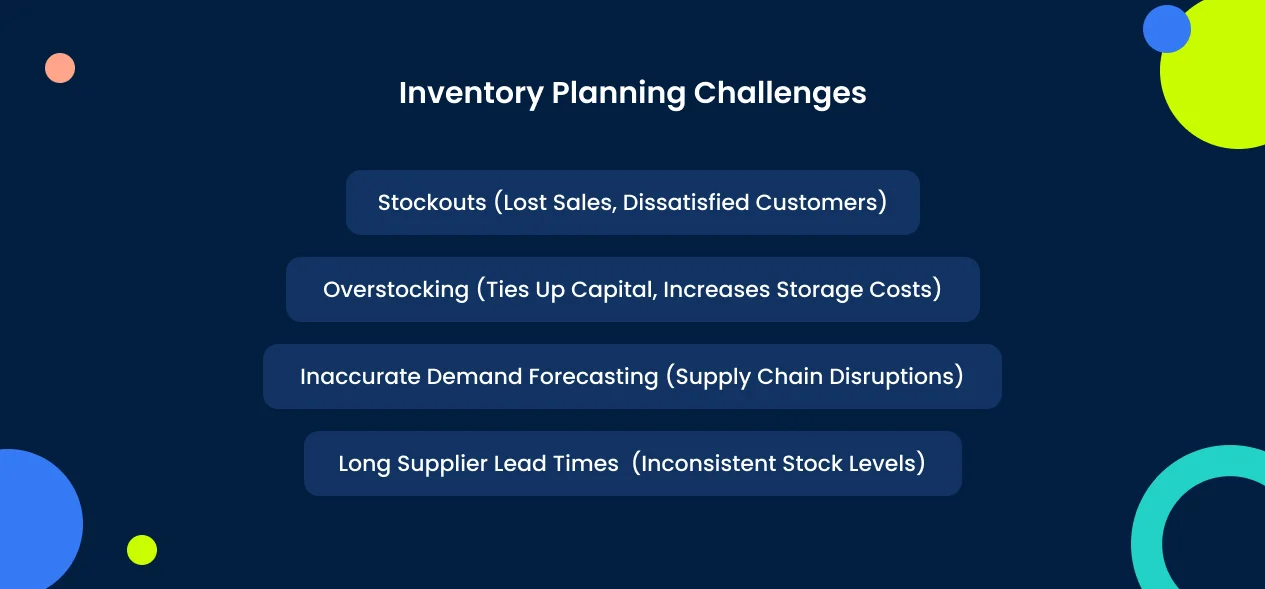
So, what helps you solve these inventory challenges? Replenishment planning.
Replenishment planning helps tackle these challenges through a structured approach to inventory management:
- Accurate demand forecasting: Ensures products are available when needed, reducing the risk of stockouts.
- Automated stock tracking: Monitors inventory levels in real-time, simplifying the replenishment process.
- Reduced overstocking: Prevents excess inventory, lowering storage costs and freeing up capital.
- Lead time management: Accounts for supplier delays, ensuring timely restocking to avoid disruptions.
- Improved operational efficiency: Streamlines inventory processes, saving time and reducing manual errors.
8 Best practices for stable inventory replenishment planning
Now let’s go through best practices that can make your inventory replenishment planning easier:
1. Use data-driven forecasting
Accurate predictions are key to efficient inventory management.
It helps you avoid overstocking or stockouts by aligning inventory levels with anticipated demand.
Analyse sales trends, market conditions, and historical data to estimate future demand, which can help you maintain balanced stock levels.
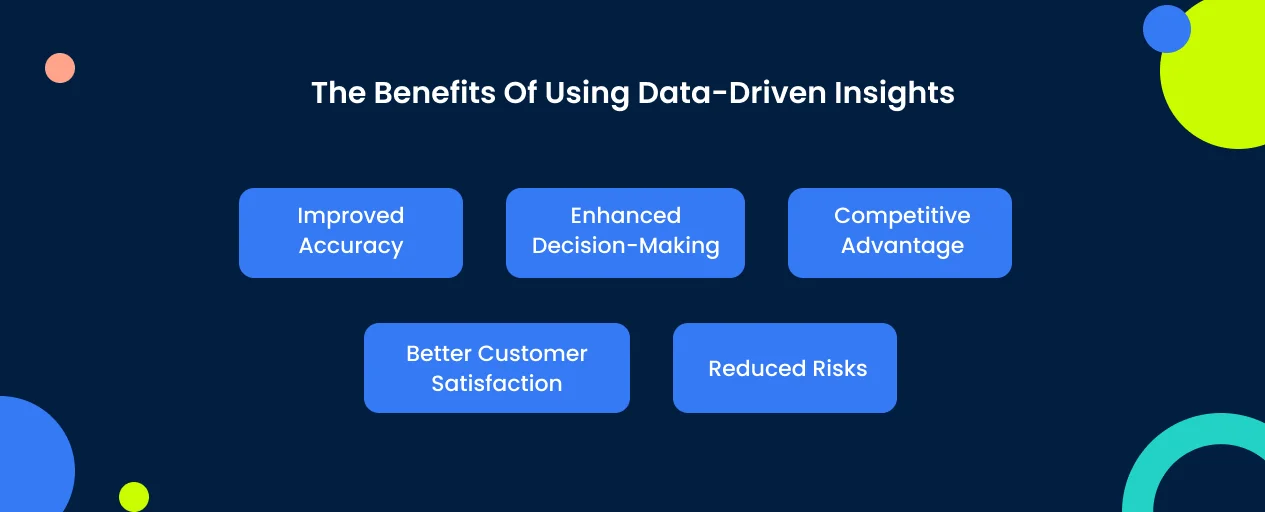
This approach ensures your inventory strategy is always one step ahead by:
- reducing risks,
- improving decision-making accuracy,
- enhancing customer satisfaction,
- and providing a competitive advantage.
2. Aim for ideal stock levels
Strive to achieve the perfect balance between supply and demand by focusing on accurate forecasting and timely replenishment.
Instead of relying on buffer stock, which can lead to overstocking and unnecessary costs, use real-time inventory data and demand trends to guide your decisions.
This approach helps minimize waste, optimize cash flow, and maintain product availability, ensuring you meet customer needs while avoiding the pitfalls of excess inventory.
Pro tip
Fabrikatör’s replenishment feature helps optimize stock levels by using AI-powered algorithms to analyze demand patterns, lead times, and stock coverage metrics.
Users can set up customized replenishment rules based on their supply chain needs, including ideal reorder points and quantities. Once configured, the tool automates the restocking process, ensuring timely replenishment and reducing the risks of stockouts or overstocking.
3. Use proven inventory management techniques
You can optimize your replenishment strategies by leveraging established inventory management techniques, each addressing specific needs and challenges. Here's an overview:
1️⃣ ABC analysis: Categorise inventory into three groups:
- A items: High-value, low-quantity best-sellers that generate 80% of the revenue.
- B items: Moderate-value products with steady sales, generating 15% of the revenue.
- C items: Low-value items that are less critical, generating 5% of the revenue.
This helps you prioritize resources for the most impactful products.
2️⃣ Just-in-time (JIT) inventory: Order stock only when needed to reduce storage costs and minimize waste, ensuring efficient inventory flow.
3️⃣ Economic order quantity (EOQ): Determine the optimal order quantity to balance ordering and holding costs while maintaining efficient inventory levels.
4️⃣ Batch tracking: Monitor inventory batches to improve traceability, ensure quality control, and manage product recalls effectively.
5️⃣ First-in, First-out (FIFO): Sell older inventory first to prevent spoilage, especially for perishable or time-sensitive items.
6️⃣ Vendor-managed inventory (VMI): This option allows suppliers to manage and replenish your inventory, improving collaboration and reducing stockouts.
4. Simplify replenishment processes
Streamlined replenishment saves time and reduces errors.
By leveraging automated replenishment tools, you can ensure that purchase orders are created and processed seamlessly as soon as stock levels reach a predefined threshold.
This means setting up systems that monitor your stock levels in real-time and automatically initiate restocking processes when inventory falls below a predefined threshold.
These tools use data like sales trends, lead times, and reorder points to determine the optimal time to place a new order.
When stock levels drop to a critical level, the system generates purchase orders and sends them to suppliers without requiring manual intervention.
Pro Tip
Fabrikatör's purchase order management feature automates procurement by integrating with Shopify to provide data-driven insights from forecasts, incoming inventory, and sales trends.
It forecasts demand, tracks incoming inventory, and automates backorders to optimize purchasing and maintain customer satisfaction.
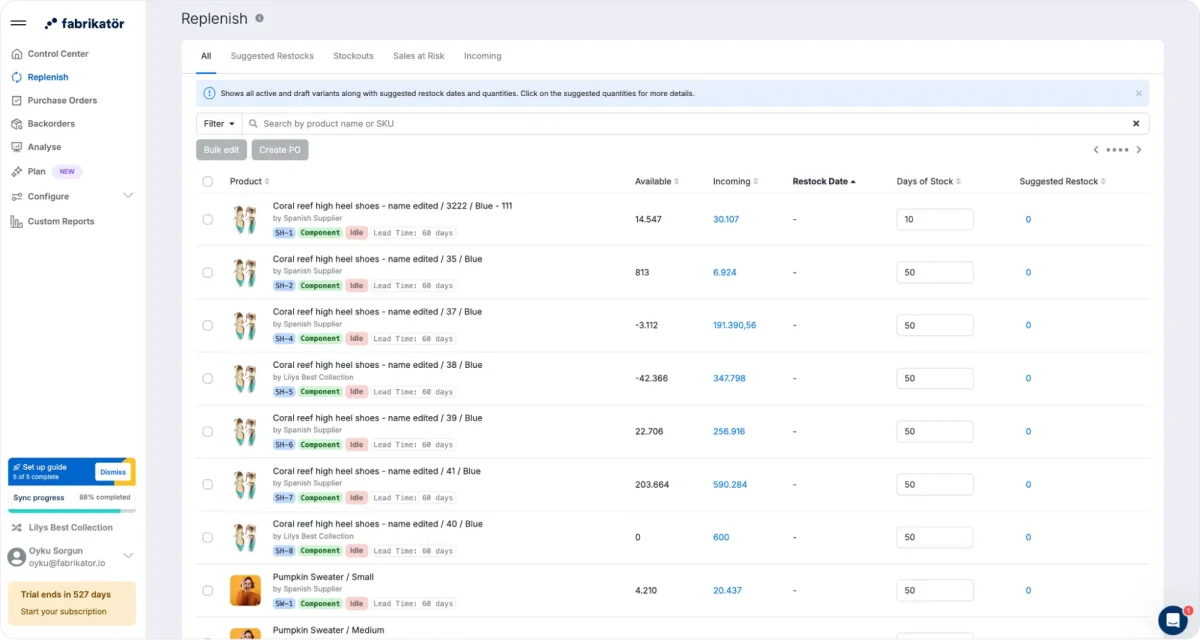
This automation reduces manual errors and ensures timely restocking, leading to optimized purchasing processes and a consistent inventory flow.
5. Align replenishment with product life cycles
Inventory needs vary depending on where a product is in its life cycle.
Plan for key stages such as:
- Manufacturing and lead times to avoid delays.
- Customer demand shifts as products peak or decline.
- New product allocations to support launches effectively.
Adjusting replenishment strategies based on the product life cycle ensures smoother operations.
6. Build strong supplier relationships
Effective collaboration with suppliers can prevent delivery delays and reduce inventory issues.
Communicate changes in schedules promptly and coordinate delivery times to avoid bottlenecks.
Establish practical service levels to ensure timely, safe, and efficient replenishment.
7. Minimize stockouts with proactive measures
Stockouts not only result in lost sales but can also damage customer trust. Use these strategies to avoid them:
- Utilize accurate demand forecasting tools.
- Perform regular cycle counts to verify inventory.
- Implement strict quality control measures to reduce errors.
8. Continuously improve your strategy
Inventory replenishment is dynamic, and maintaining its effectiveness requires regular evaluation and adaptation.
To achieve this, it’s important to consistently review key performance metrics, adjust to market changes as they arise, and implement improvements that ensure your strategy stays effective and relevant.
To improve your strategy, you can:
- Analyze sales data to spot patterns and identify which products need more attention.
- Monitor market trends to anticipate shifts in demand and review lead times or supplier performance to address potential bottlenecks.
- Gather feedback from your team or suppliers to highlight inefficiencies or areas for improvement, ensuring your replenishment plan remains responsive and effective.
How to implement replenishment planning
To implement replenishment planning, start by assessing your current inventory management practices and identifying areas for improvement.
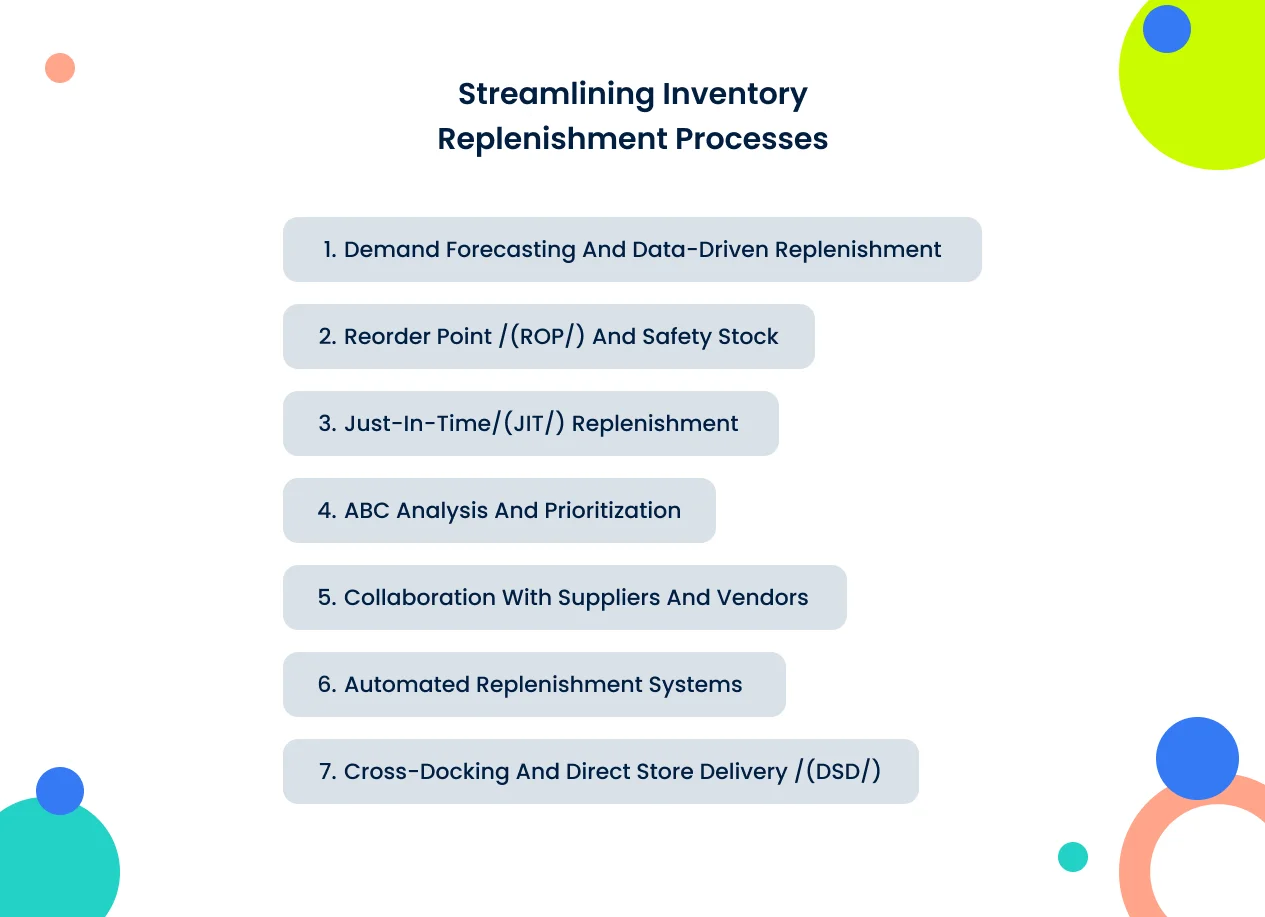
Set clear goals, such as reducing stockouts or minimizing excess inventory, and establish a forecasting, tracking, and automation process.
Let’s dive deeper into the steps for implementing replenishment planning.
Step 1: Assess your current inventory management practices
Understanding your current inventory management practices is crucial because it allows you to pinpoint inefficiencies and uncover areas for improvement.
This step sets the foundation for a more streamlined and effective replenishment strategy.
That’s why it's important to evaluate your current inventory management practices and identify inefficiencies like:
- stockouts,
- overstocking,
- or delays,
While reviewing:
- tracking,
- ordering,
- and supplier monitoring processes.
Step 2: Define your inventory management objectives
Setting clear and measurable objectives is essential for creating a focused and effective replenishment plan.
Well-defined goals help you stay aligned with your business priorities, whether reducing costs, improving customer satisfaction, or optimizing stock levels.
Set clear, measurable goals for replenishment planning, such as reducing stockouts, minimizing excess inventory, improving customer satisfaction, or cutting storage costs.
Step 3: Gather and analyze data
Data is the backbone of a successful inventory replenishment strategy.
By analyzing sales trends, supplier performance, and current inventory levels, you gain valuable insights that help you make informed decisions and predict future needs.
Collect relevant data to support your replenishment planning.
- Sales data: Identify trends and seasonal patterns.
- Supplier performance metrics: Review lead times and reliability.
- Current inventory levels: Assess stock turnover rates.
Step 4: Choose the right tools and technology
Investing in the right tools and technology enhances accuracy and efficiency in inventory management.
However, choosing the one that fits your needs can be challenging if you haven’t used one before.
Features like demand forecasting, real-time tracking, and automated reordering can help you stay ahead of demand and reduce manual errors.
For example, Fabrikatör offers a comprehensive solution that optimizes stock management processes.
Some of the key features it includes are AI-powered forecasting, adaptive replenishment, and real-time inventory visibility, allowing you to keep your orders optimized, reduce stockouts, and maintain seamless inventory flow.
Using Fabrikatör can help you streamline operations, minimize errors, and easily maintain ideal stock levels.
Step 5: Develop your replenishment plan
A well-structured replenishment plan ensures you’re prepared for fluctuations in demand and supplier lead times.
By incorporating safety stock levels and reorder points, you create a system that balances inventory levels while minimizing disruptions.
A flexible and well-structured replenishment plan ensures your strategy is effective, incorporating safety stock levels, reorder points, supplier lead times, and the ability to adapt to market changes or unexpected demand spikes.
Step 6: Train your team
Your replenishment strategy is only as strong as the team implementing it.
Proper training empowers your staff to use inventory tools effectively, interpret data, and follow new processes, ensuring seamless execution of your plan.
Educate your team on the new replenishment processes and tools by providing training on using inventory management software, interpreting data, and implementing the plan effectively.
Step 7: Implement, monitor, and adjust
Implementation is where your planning turns into action, but regular monitoring ensures your strategy delivers results.
Using KPIs to track success and adjusting as needed keeps your inventory replenishment process responsive and effective over time.
To do this:
- Implement your replenishment plan to put your strategy into action.
- Monitor performance using key KPIs like stock turnover rates, fill rates, and order accuracy.
- Adjust the plan to address inefficiencies or adapt to market changes, ensuring continued effectiveness.
How can Fabrikatör elevate your inventory management?
Fabrikatör is an advanced inventory management platform designed to optimize supply chain processes for Shopify users.
Our intelligent replenishment tool ensures your inventory decisions are based on accurate data, eliminating the need for manual calculations and reducing the chance of human error.
You can maintain optimal stock levels and improve efficiency with automated suggestions tailored to your supply chain metrics.
Here’s how Fabrikatör’s replenishment planning works:
- Custom rules: Define replenishment rules such as lead times, stock coverage, and supplier details to generate precise restocking recommendations.
- Seamless ordering: Convert restocking suggestions into purchase orders with a single click, streamlining the process.
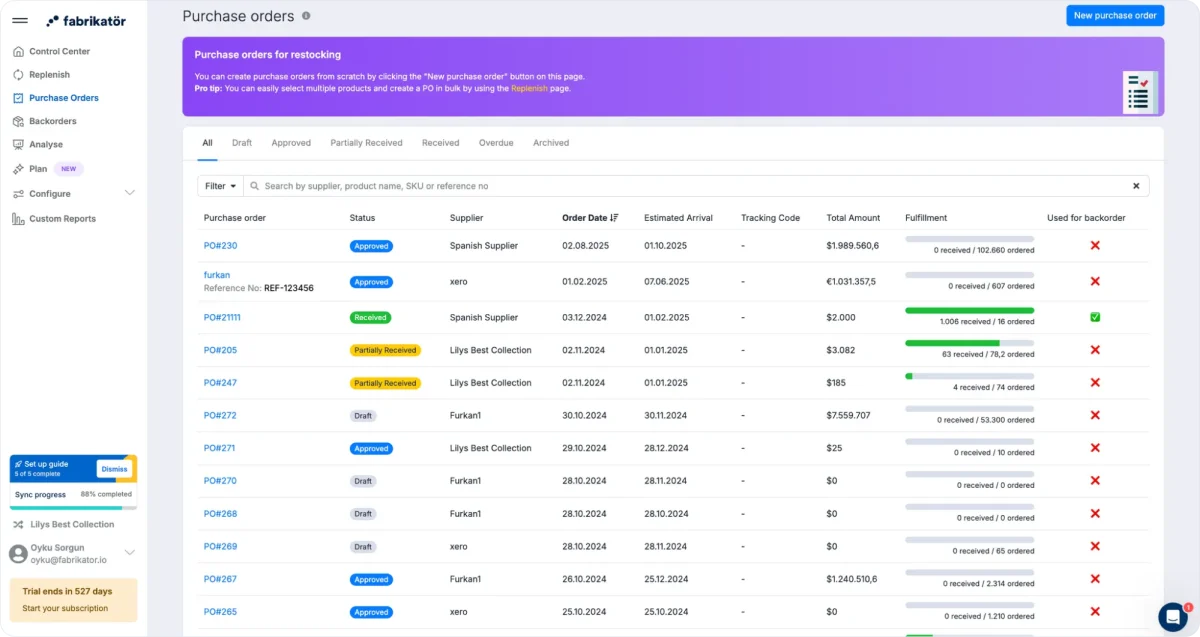
- Backorder automation: Enable backorders to continue selling out-of-stock items while en route, helping you recover lost sales and maintain customer satisfaction.
Besides the replenishment feature, we can additionally offer:
- Advanced forecasting: Leverage growth rates or AI algorithms to predict future demand based on past sales, seasonal patterns, and marketing events, ensuring accurate planning and restocking.
- Real-time analytics: Access 100+ metrics to monitor inventory, sales trends, and supply chain performance, empowering data-driven decisions.
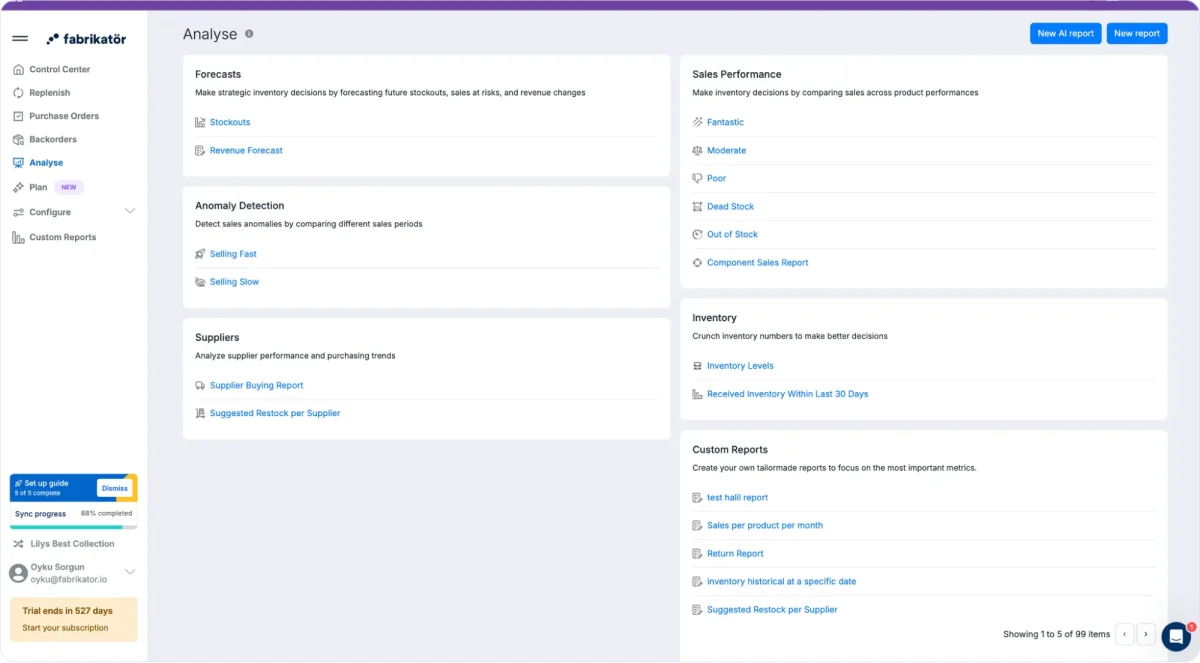
- Optimized freight planner: Compare freight options, balancing speed and cost to maximize savings without compromising efficiency.
- E-commerce platform integrations: Integrate seamlessly with Shopify and Shopify Plus to optimize inventory management across your sales channels.
- Financial and operational tools integrations: Connect with QuickBooks, Xero, and ShipHero to streamline financial processes and logistics.
- Analytics and custom workflow integrations: Enhance insights and communication with Klaviyo for tailored workflows.
Curious about how effective inventory replenishment planning can transform your business?
Try Fabrikatör or get a demo, and transform your inventory planning and management with advanced analytics, automated workflows, and smarter purchasing decisions.